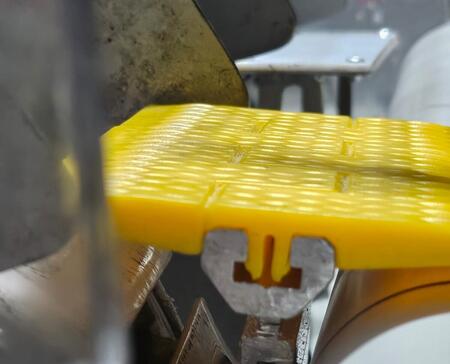
Industry
Food Processing – Packaging
Application
Coffee and Milk Powder Packaging
Product
Segmented Transfer Plates
Objective
Decreased product damage, decreased downtime
Conveyor Details
Belt type: Modular/PVC
Problem:
A major food industry packaging plant located in Southeast Asia was experiencing excess rips and tears of the sachets moving throughout their belt conveying process, especially across their belt-to-belt transfer points. As a result, many of their sachets were deemed unable to ship, and their rejection rate was slowly creeping higher and higher. After some time, their plant maintenance team decided to implement a homemade solution to help them smoothly glide between belts. However, the edge of their installed plate would quickly deteriorate and become sharp, cutting through the packaging and creating yet another mess that their team needed to clean up. The plant manager was becoming increasingly worried about damaging their relationships with their consumers, so they decided it was time to find a better, more specialized solution.
Solution:
After researching local belt conveyor solutions providers, their plant manager decided to host a Flexco Territory Manager for a site walkthrough. Before the meeting, their team was under the impression that something like a food grade belt cleaner might be the right solution due to the dusty nature of their food processing application. Once on site, though, it became incredibly evident that Flexco’s Segmented Transfer Plates (STPs) would be immediately effective as they are ideal for packaged food applications. By lying flat between belt transfers, STPs extend across the length of the belt and allow sachets to move from belt-to-belt with limited concerns of them becoming jammed, damaged, or lost on the floor. Additionally, STP material is made from durable HDPE; this was incredibly important to their team as it would limit the likelihood of further breaking down and puncturing their packages as their previous solution had done. After further discussion, they decided to install an STP unit.
Result:
Once installed, their plant manager noticed an immediate boost in production throughput, with a measurable higher volume of packages making it out to shipment compared to the results prior to the Flexco STP installation. In the past, their maintenance team had to make monthly replacements for their homemade transfer plate, causing output to decrease due to the related unplanned downtime to reinstall their homemade plate, all while still having heaps of damaged packages to deal with. Now, with STPs installed at their key transfer points, they are able to run production without the worry of having to constantly check for damaged sachets. The sites plant manager went on to note that Flexco’s Segmented Transfer Plates have not only helped keep packages flowing, but they have also further strengthened their relationship with their customers as they can more efficiently meet their order needs with fewer delays and more inventory availability.