Foundations - The Early Years (1907-1929)
1907
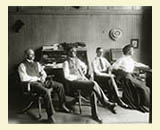
In March of 1907, George E. Purple, Albert B. Beach, and Philip S. Rinaldo founded Flexible Steel Lacing Company. The initial product line, a hinged fastener, was manufactured from a patent purchased from Olof N. Tevander of Toledo, Ohio.
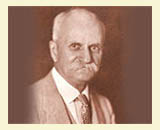
As the company’s first president, George Edward Purple initiated the company’s commitment to innovative design and continuous product development. Involved in every aspect of the business in the early years, George was a persistent and tireless inventor who developed 19 registered patents related to conveyor belt technology. George served as the president until his untimely death in 1930.
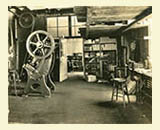
The first Flexible Steel Lacing Facility at 71 W. Jackson in Chicago doubled as both a small office and workshop.
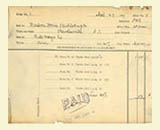
By May of 1907 Purple, Beach, and Rinaldo had landed their first sale for one dollar and twenty-two cents to the Western Home Ventilation Company in Bartlesville, located in an Indian Territory that would become Oklahoma. Sales for the first year amounted to $5500. Very early on, these men made the commitment to sell through distribution, and records show the first distributor contact in November 1907.
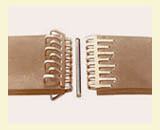
Overcoming the shortcomings of the original Tevander design, the original fastener was soon modified to a separable joint with loops from both ends of the belt intermeshed and joined by a rawhide hinge pin.
1909
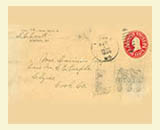
George Purple created a modified turned tooth design, mailing himself a letter with the design drawing on the envelope to record the date. An additional patent added a second, shorter tooth and finalized the design. When it was viewed from the side, it resembled the open jaws of an alligator … and so, ever since its introduction in 1909, this design has been known as Alligator® belt lacing.
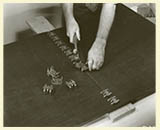
Using the proven performance principles of the redesigned Alligator lacing, George Purple developed the Turtle fastener. Designed as a series of drive-on plates used for troughing conveyors, the Turtle fastener is still used today, primarily for rip repair.
1915
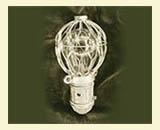
One of Flexco’s few non-belt maintenance products – the stamped metal lamp guard, trade-named “Flexco-Lok” – remained in the product line until the 1950s when they were replaced with guards produced from metal wire. The most interesting application for this product was its use in the production of the liberty ships constructed by the War Department in 1941 just prior to the attack on Pearl Harbor.
1919
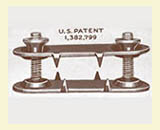
B.F. Goodrich called upon Flexco after producing two-inch thick belt for an open-pit copper mine in Chile. The inability to vulcanize in this area led Goodrich to specify the use of mechanical belt fastening, but none existed that met the belt specifications. Patented in 1919 and designed as a compression fastener, the Flexco® HD® single plate fastener used high tensile-strength bolts to draw the plates together. The fastener is still sold today as our Flexco® Bolt Solid Plate No.3. The cooperative joint-effort between belt manufacturer and fastener manufacturer set a precedent that is today an industry practice.
1921
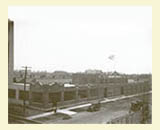
In 1921 the company built a new plant at 4607-31 Lexington Street. The building had a two-story office with 40,000 square feet of manufacturing space. By this time, Flexco employed 79 people, operated 17 presses and consumed more than 30,000 pounds of steel weekly. Today the old plant can still be seen from Chicago’s Dwight D. Eisenhower Expressway.
1920s
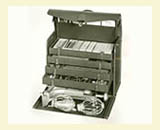
Pictured is a Flexco salesman’s sample case from the 1920’s. Throughout these early years, Flexco developed strong relationships within the industry through its field sales force. In 1923, the company held its first annual sales convention – by this time the sales force numbered 11. Hugh Coats, the company’s first sales representative and sales manager, felt the convention would give the representatives a sense of belonging to a substantial company, to see the new factory and meet with the officers in person.
1928
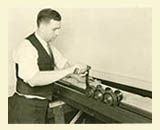
Milton Beach, the company’s fourth president, is shown demonstrating the Alligator® Roll Carriage lacing machine. In 1928, George Purple recognized the need for installing large quantities of lacing with a simple, hand operated machine. Original equipment manufacturers and large volume consumers could pre-lace belts for more efficient installation of mechanical fasteners.
The Growing Years (1930-1970)
1930s
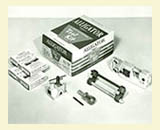
As the 1930s began, flat transmission belts were starting to be replaced by V-belts. As a result of this shift, Flexco introduced a combination of a hinged V-belt fastener and special V-belting. Marketed under the strong brand name of Alligator®, the fasteners quickly became, and are still, the accepted method for joining open-end V-belt. Over the years, more than 20 patents have been granted relating to Alligator V-belt fasteners.
1931

Hugh Beach was elected the company’s third president. As the eldest son of founder A.B. Beach, he had joined the company in 1912 and was amply prepared for leadership. Hugh Jay Beach was the first of the “next generation” to lead Flexco and he saw the company through both the Depression and World War II, ensuring that employees were valued for their contributions to that effort as well. Throughout these growing years, focus on technical expertise, strong communications efforts, and innovation in product development continued to be a driving force for Flexco.
1946
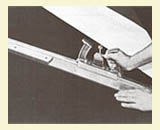
As wider conveyor belts became more common in the 1940s, the need for an improved cutting tool that could safely and accurately cuts these belts became apparent. The Alligator® Wide Belt Cutter was developed and patented as Flexco’s answer to safety and the need for a straight cut. The belt maintenance products the company produces today still focus on worker safety and efficiency.
1947
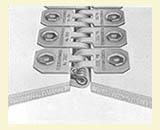
The need for a heavy-duty, mine-suitable fastener provided an opportunity for Flexco. The rapidly moving, continuous mining method required an easily extendable haulage system. The Flexco® 500 was introduced as a hinged bolt fastener. The finished splice could be easily separated and rejoined in the mine shaft to allow lengthening of the belt of the on-the-spot repairs. In addition, it could be applied without hauling heavy machinery around the mine. The compression grip and large hinge pin ensured maximum splice strength in most belts. Later renamed #550, the product is currently used on construction equipment and in a variety of other bulk haulage applications.
1949
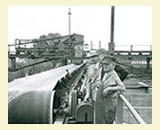
Here, Hugh Beach is seen with the maintenance crew of Ohio River Sand. After World War II ended, development of the U.S. Interstate Highway System required tremendous amounts of sand and crushed stone, which meant an increased number of conveyors needed to process these materials. The highly abrasive nature of these materials, coupled with the sudden growth in the aggregate industry, provided a significant opportunity for Flexco® Bolt Solid Plate Fasteners.
1953
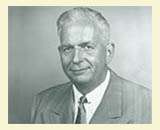
Milton Beach joined Flexco in 1923 as a mechanical draftsman and managed critical periods in company history with devotion to product and process refinement. He set high benchmarks for our technical leaders to follow – his focus … "to make it as good or better than we used to make it." In 1953 Milton was elected president – he paved the way for the 1960s and the next generation of leadership.
1958
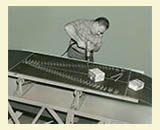
The Wedlok® V-shaped splice was developed to meet the need for a higher tension mechanical splice in belts designed for vulcanization – belts without the cross yarns needed to hold a conventional mechanical splice. Windy Pray, Flexco’s Chief Development Engineer, was heavily involved in the Wedlok development program and is shown in this picture installing a splice.
1964
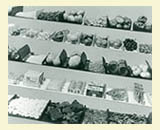
Flexco purchased a controlling interest in Tatch-A-Cleat®, the company’s first subsidiary. The California based manufacturer of belt cleats broadened the company’s involvement in belt-related products. In 1987, Tatch-A-Cleat became a wholly-owned subsidiary of Flexco.
1965
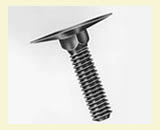
The company identified the need for dependable, high quality grain elevator bucket bolts. Flexco redesigned the traditional Norway style bolt to be compatible with reduced ply synthetic fabric belting.
1966
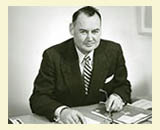
John P. Ramsey, son-in-law of founder Philip Rinaldo Sr., joined Flexco in 1941 and was elected president and chief operating office in 1966. He led the company through continued product development and growth, honing the skills of the sales force and researching the potential for technology in the workplace. The management of Flexco during this time, especially John, were acutely aware of the need to broaden the product lines and under his leadership, the company added elevator bolts, silicone rubber-cutting lubricant, and Tatch-A-Cleat®. In 1974, John retired from active management of the company.
1968
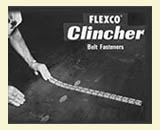
“Select Clincher in ‘68” was the promotional slogan tied to the election year campaign as the new Clincher system was presented to the field sales group at their November sales convention. Clincher was proposed as a solution for lightweight synthetic carcass belting that operated over small diameter pulleys. The finished splice would be comprised of a set of hinged plates secured on the belt with stainless steel staples. In 1977, the Clincher staple fastener line was redesigned and renamed Alligator® Staple.
New Directions (1971-1989)
1971
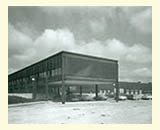
In 1971 the company’s plant and offices were relocated to a 10 acre site in Downers Grove, Illinois. Employment at the new facility was expected to increase to 150 full time associates. The new factory included air conditioning, skylights, eye-level windows, wide aisles, and a Flexco family atmosphere with a common door and cafeteria for both office and factory workers. In 1981, the first significant expansion of the factory took place and increased the plant size to 155,000 square feet. Two years later, a new training center was added to Flexco headquarters.
1972
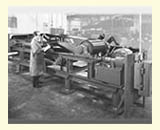
In the 1970s acceptance of straight-warp belting was growing in the coal mining industry. During that time, Uniroyal, Inc., one of the belting manufacturers that pioneered straight-warp belting, was experimenting with a fastener applied with rivets. Preferring not to go into the fastener business, Uniroyal offered its ideas and product to Flexco. After further design refinements were made, Flexco introduced the R5 Rivet Fastener at the 1972 Coal Show. The rivet fastener allowed a quick and simple installation that worked reliably under high tensions and on belts with straight-warp construction.
1974
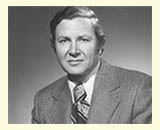
Alfred E. Gladding began his career with Flexco in 1956. He was elected president in 1974. During 16 years of leadership, he expanded the R&D department and spearheaded the development and introduction of a number of new products. Product innovation continued as Flexco moved forward in recognizing the need for a global orientation in both design and product mix. Al’s early initiatives in traveling worldwide and developing business relationships served to enable subsidiary acquisitions that characterized the 90s and led to significant growth in worldwide sales and distribution. He retired in 1990.
1976
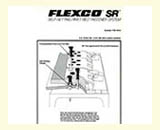
While the R5 splice proved to be a solid solution for the mining industry, the installation process of driving and setting rivets was laborious. Flexco used technical expertise and customer-focused vision to improve rivet installation by providing a unique, pre-assembled rivet to minimize on-site installation time. The combination of the rivet and pilot nail and special tooling allowed the rivets to be "self-setting." It was patented in 1976 and is one of the most valued patents in Flexco’s history.
1983
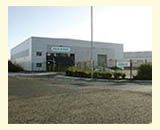
Flexible Steel Lacing (UK) Ltd. was established as Flexco’s first international subsidiary located in Manchester, England.
1984
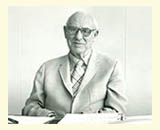
In the summer of 1984 Philip S. Rinaldo Jr. Retired at age 79. Phil came to Flexco in 1930, working in accounting, finance, and export. He served many years as Chief Financial Officer, Executive VP, and as chief advisor to four Flexco presidents. Working with Hugh Beach in the early 1940s, he was instrumental in developing our export relationships and continued his export and international involvement for over 50 years. At the time of his retirement, Flexco was actively exporting to over 75 countries.
1987
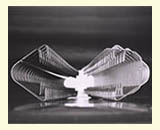
The Gator® line of wire hooks and lacers was officially launched at a special mid-year sales meeting in 1987. Flexco had partnered with the Wilhelm Sülzle Company of Germany to private label its Anchor product line under the “Gator” brand, a twist on the successful Alligator® trademark.
1987
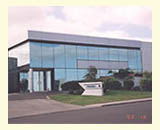
Flexible Steel Lacing NZ Ltd. was established as Flexco’s second international subsidiary located in Auckland, New Zealand. In 2001, the Auckland warehouse was closed and field salesmen began reporting to regional sales management in Sydney, Australia.
Global Foundations (1990 - 2007)
1990
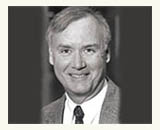
Peter M. (Mick) Ramsey became Flexco’s seventh top executive in 1990. During the nearly 35 years, Mick was employed at Flexco he, like the three generations of leaders before him, chose to focus on the potential for product sales outside the United States. In May 2001, at the annual Shareholders weekend, Mick Ramsey retired from operational responsibilities with the company.
1991
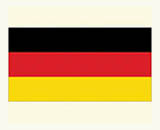
In April of 1991, four years after the beginning of the importation of Anchor belt hooks from Germany, Flexco and the Wilhelm Sülzle GmbH formed a joint partnership called Anker-Flexco. The facility is located in Rosenfeld, Germany.
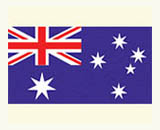
Flexco’s fourth international subsidiary, Belle Banne (Australia) Pty. Ltd., was formed. The acquisition included Belle Banne pulley lagging and belt cleaner product lines, which are currently marketed around the world under various trade names. The subsidiary is called Flexco (Aust) Pty. Ltd. and is located in Baulkham Hills, New South Wales, Australia.
1992
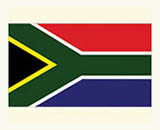
April 1992 marked the formation of Flexco’s fifth subsidiary, Flexible Steel Lacing (S.A.) (Pty) Ltd., in the Republic of South Africa.
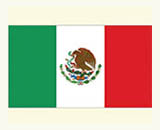
As early as 1947, Flexco has been represented Mexico. In 1992, Flexco de Mexico SA de CV was formed as Flexco’s subsidiary located in Mexico City, Mexico.
1994
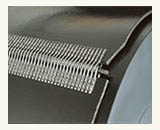
Flexco® Staple fasteners were introduced. The stainless steel narrow plate fasteners are machine applied and provide a long wearing, abrasion-resistant solution in corrosive mining environments. The narrow rounded loops help extend hinge pin life, and the beveled edges of the plates provide a smooth transition of belt cleaners.
1995
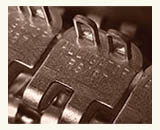
One of the most significant developments of its time was the Alligator® Ready Set™ fastener system. In contrast to the individual loading of staples in the Clincher and Alligator Staple lines, Ready-Set fasteners have the staple pre-staked into the top plates. All that is needed is to drive the staple through the belt and “finish” the splice on a steel plate. Ready-Set was patented in 1995 in the U.S. and abroad, and is today one of Flexco’s highest growth product lines.
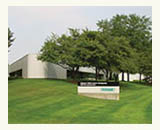
In 1995, Flexco acquired Clipper Belt Lacer Company in Grand Rapids, Michigan. The partnership was a mutual benefit – Clipper joined a well-financed, worldwide marketing organization and Flexco gained an adaptable world class manufacturing plant.
1998
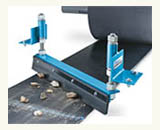
In 1998 Flexco began manufacturing the Belle Banne style belt cleaners in its Grand Rapids facility. A full range of products was envisioned for the Belt Conveyor Products group including belt trackers, plows, and several lines of belt cleaners. This vision has become a reality as production and marketing of the Belt Conveyor Products line exceeded 25% of overall sales in 2006.
1999
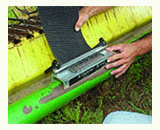
Developed as a higher tension fastener for round hay balers, the Alligator® Rivet Fastener was introduced in 1989 and production installation machines were placed at two original equipment manufacturers.
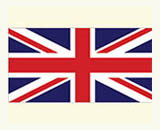
Flexco acquired Jackson Fastener Ltd. in 1999. Originally founded in 1879 as a manufacturer of fasteners for power transmission belts, at the time of the acquisition, the company manufactured elevator bolts and a copy of the Flexco® Solid Plate Fastener.
2001
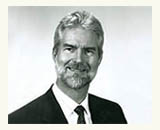
Jerome S. Paulson was elected the company’s eighth president in 2001. In his long and varied career with Flexco, Jerry was an innovator, change agent, and coach. In a true reflection of his mentor, Phil Rinaldo, Jerry got his greatest satisfaction from empowering others. On May 7, 2005, Jerry Paulson retired.
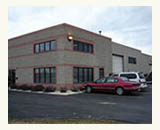
The Parramatta Group, located in Plainfield, Illinois, was established as a separate division for the design, engineering, and marketing of Belt Conveyor Products in North America. In 2004 it became the North American division for the introduction of Controlled Flow Material Transfer System™ technology from the Tasman-Warajay Company in Australia.
2003
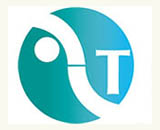
Flexco acquired Tasman-Warajay, a design and fabrication firm in Queensland, Australia, specializing in controlled flow conveyor transfer chute technology. Since 1983, Tasman-Warajay has had its systems in place at Australia’s busiest port load-outs – eliminating dust and increasing production with proprietary technology.
1994

In 1994, an innovative new version of the Flexco® Solid Plate Fastener was introduced. Called Flexco VP™, the product entailed a group of bolt solid top plates molded into a 6” wide strip. When it is installed on a skived conveyor belt, the “countersunk” splice lies flush with the belt for a smooth top profile.
2004
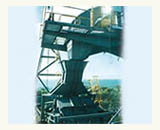
The Controlled Flow Material Transfer System™ was introduced in 2004 to coal prep and coal fired power plants in North America. The system provided for a globally-proven solution to excessive dust, spillage, and chute plugging. Today the systems are installed around the world.
2005
In May, 2005, Rick White was elected Flexco’s ninth President. Rick joined Flexco in 1986 as the company’s first Marketing Manager. During the 1990s, he worked closely with Mick Ramsey in the development of international markets. During Rick’s tenure, the company’s total sales have grown almost 10-fold, with international sales increasing from 12% to 50% of total revenue
2007
Flexco celebrated its 100 year anniversary on March 27, 2007.
The Next Century (2008 - Today)
2008
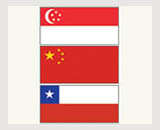
Early in 2008, Flexco-Singapore was established to service the Southeast Asia region, as well as servicing the Taiwan, Japan, and South Korea markets. Flexco continued to expand international operations that same year with the opening of manufacturing and distribution facilities in the Songjiang District of Shanghai, China and Santiago, Chile.
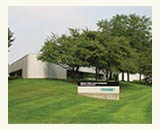
Flexco expands their Grand Rapids manufacturing facility by adding an additional 60,000 square feet of space to the already 152,000 square foot facility. Included in the expansion was a 3,500 square foot training center.
2009
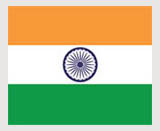
Flexco opened its 10th subsidiary location in India. Located in Chennai, the wholly-owned subsidiary provided the opportunity to maintain local stock and expand the network of sales and distribution. Flexco began developing the market for India in 1996 when they partnered with their first two distributors to support local Flexco sales.
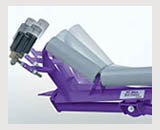
In 2009, Flexco introduced the PT Max™ belt trainer with it’s patented “pivot and tilt” mechanism. Unlike conventional pivot-only devices used to simply steer the belt, the PT Max utilized special sensors to detect belt wander and then guide the belt back to the correct path. The technology was so widely accepted, Flexco continued to add to the PT family with PT Smart™, PT Pro™, and PTEZ™.
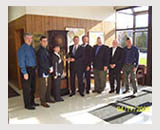
On April 16, 2009, Flexco celebrated their 100-year partnership with Troy Belting in Watervliet, New York. Flexco and Troy stand by the core values of their respective founders by maintaining key industry partnerships to more effectively serve the needs of their customers. Additional 100-year milestone partnerships continue to be celebrated as Flexco moves along in their second century of business.
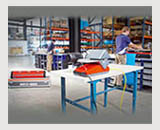
Flexco added the Novitool® line of endless splicing products to its mix of products. The line included the revolutionary patented Aero® Splice Press with integrated air cooled technology, the Ply 130™ Ply Separator, the Pun M™ Mobile Finger Punch, and the patented Amigo™ Monolithic Splice Press – a complete complement of tools for splitting, punching, and splicing to create a truly seamless endless splice.
2010
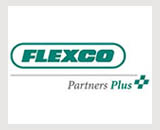
Flexco products are most effective when they’re installed and maintained properly. The launch of the Partners Plus Program allowed Flexco to share its expertise with key distributors and train them in correct installation, service, and more to ensure their mutual customers had access to expert local service and support.
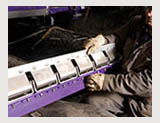
With the understanding that proper servicing of cleaners was key to ensuring effective and long-lasting performance, Flexco designed a version of their MHS belt cleaner with a new feature, the patented Service Advantage Cartridge. The slide-out design meant blades could be changed in only a matter of minutes without removing the complete assembly pole or brackets from the conveyor. Today, many of Flexco cleaners utilize the cartridge enhancement to simplify maintenance.
2013
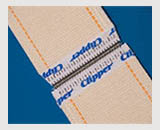
Up until 2013, the process of binding laundry tape and installing wire hooks were two different processes. With the introduction of the Clipper® Laundry Patch Fastener System, a single installation process installs the fasteners while simultaneously heating and activating the glue on the inside of the patch. From hours to seconds, the entire Clipper® patch process for laundry tape binding now takes only 20 seconds.
2015
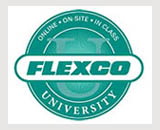
Flexco launches the online segment of Flexco University with flexcouniversity.com. The online training tool provides users access to all levels of belt conveyor training from conveyor basics to best practices and troubleshooting. The online addition combines with the established on-site and in class training programs offered by Flexco experts around the globe.
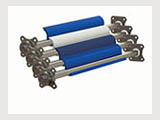
Flexco introduced the FGP Food Grade Precleaner. FDA-approved and USDA-certified to meet the highest standards for food processing applications, the FGP can be disassembled in less than a minute for regular cleaning and sanitation.
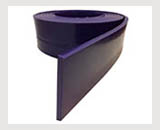
Flexco added urethane capabilities to its manufacturing process in Grand Rapids, Michigan. The investment in the equipment and resources gave Flexco the opportunity to put the highest quality urethane cleaner blades on the market. With the success of the blades, Flexco continued to invest in manufacturing capabilities to bring other innovative, custom urethane products to market.
2016
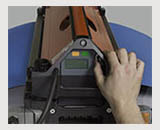
Significant product advancements to the Novitool® Aero® Splice Press allowed Flexco to be first to market with an air-cooled press that incorporated an exclusive Recipe Management Tool. Users can import, create, or modify endless splice recipes and ensure consistent, high quality splice performance from operator to operator, and from tool to tool, for any specified splice parameter.
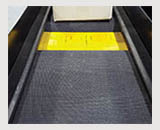
Flexco introduced two transfer solutions designed to provide smooth transitions of product over conveyor hitches and transfers. The patented Segmented Transfer Plates and Hitch Guards are designed to prevent product and foreign object debris from jamming in the transfers, minimizing product and belt damage, increasing efficiency, and eliminating costly downtime in parcel handling operations.
2017
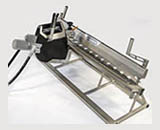
Flexco launched the new Flexco® XP™ Staple Fastening System in China. The patented XP Staple System combined an enhanced hydraulic applicator tool with the longest-wearing staple fastener and hinge pin on the market. Designed for use with solid woven PVG/PVC and ply belts, the Flexco XP line was quickly expanded to include a manual applicator tool and multiple fastener sizes, and is now sold around the world for use in the toughest mining applications.