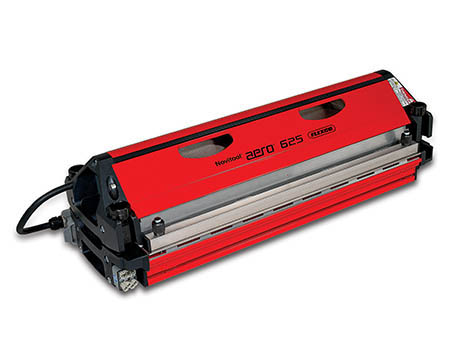
Industry
Industrial Baking
Application
Candy bar line
Product
Novitool® Aero® Splice Press
Objectives
Reduce downtime
Reduce manpower and maintenance costs
Increase sanitation
Conveyor Detail
2-ply polyurethane food grade belting
Problem:
A large candy manufacturer in India was bringing in an outside contractor to splice belts using a water-cooled press. Belt preparation and splicing was taking six to eight hours with a crew of four people. While the process was working, it was costing the manufacturer precious production time because the crew had to remove the belt from the conveyor to bring it to the heavy, water-cooled press for splicing, and then realign the belt on the conveyor to get it back up and running.
Solution:
The plant’s technical manager knew there had to be a better, faster way to get splices done, both during scheduled downtimes and in emergency situations. After some research, he contacted a local distributor to schedule a demonstration of the Novitool® Aero® Splice Press from Flexco. The portability, ease of use, and fast splice time was enough to convince him to invest in a lightweight solution that would also allow him to control the splicing process by bringing his belt splicing in-house.
Result:
The Aero Splice Press is now used at least twice a month for unscheduled downtime and for 10-15 splices at a time during scheduled downtime. A crew of two is now assigned to the Aero Press and the process takes only two hours from belt prep to cool down. Most importantly, they are able to place the lightweight Aero Press right on top of the conveyor to splice belts, instead of removing the belt and having to reinstall it on the conveyor after splicing. The operation estimates a minimum monthly savings of $5,000 thanks to the reduction in total splice time and ability to perform the splices in-house, making the return on investment time for this press very short.
In addition to the documented time savings, a potentially larger additional value came from the elimination of the water required for cooling the old press. The built-in, forced air-cooling of the Aero was noted by the site technical manager as a much more sanitary method for cooling the press.